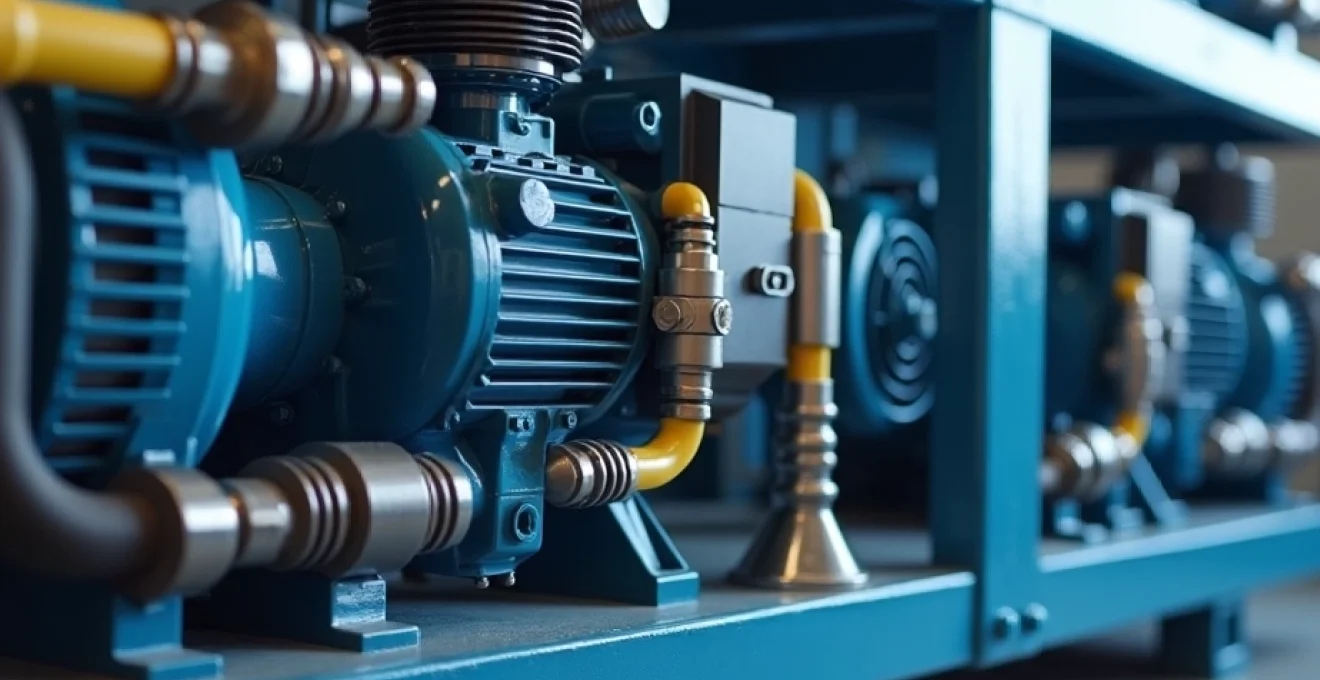
Les compresseurs d’air sont des équipements essentiels dans de nombreux secteurs industriels et commerciaux. Cependant, comme toute machine, ils sont sujets à des pannes qui peuvent perturber gravement les opérations. Comprendre les causes les plus fréquentes de défaillance permet d’optimiser la maintenance préventive et de prolonger la durée de vie de ces appareils cruciaux. Examinons en détail les principaux facteurs à l’origine des pannes de compresseurs, des problèmes mécaniques aux enjeux de qualité d’air, en passant par les défaillances électriques.
Défaillances mécaniques des compresseurs à piston
Les compresseurs à piston sont largement utilisés dans l’industrie pour leur robustesse et leur efficacité. Néanmoins, leurs composants mécaniques sont soumis à des contraintes importantes qui peuvent entraîner une usure prématurée. Identifier ces points de faiblesse permet d’anticiper les pannes potentielles.
Usure des segments et des cylindres
L’usure des segments de piston et des parois de cylindre est l’une des causes les plus courantes de perte de performance dans les compresseurs à piston. Ces composants assurent l’étanchéité entre la chambre de compression et le carter moteur. Avec le temps, la friction répétée entraîne une dégradation progressive de leur surface. On observe alors une baisse de compression, une augmentation de la consommation d’huile et une perte d’efficacité globale du compresseur.
Pour prévenir ce problème, il est essentiel de respecter les intervalles de maintenance recommandés par le fabricant. Un contrôle régulier de la compression dans chaque cylindre permet de détecter les signes précoces d’usure. Dans certains cas, un simple remplacement des segments peut suffire à restaurer les performances. Cependant, si l’usure est trop avancée, un réalésage du cylindre ou son remplacement complet peut s’avérer nécessaire.
Rupture des soupapes d’admission et de refoulement
Les soupapes jouent un rôle crucial dans le fonctionnement d’un compresseur à piston. Elles régulent le flux d’air entrant et sortant de la chambre de compression. Soumises à des cycles d’ouverture et de fermeture constants, ces pièces sont particulièrement vulnérables à la fatigue mécanique. Une rupture de soupape peut entraîner une chute brutale de pression et un arrêt complet du compresseur.
Les signes avant-coureurs d’une défaillance de soupape incluent souvent une baisse de performance, des bruits anormaux ou des vibrations inhabituelles. Une inspection visuelle régulière des soupapes, couplée à des tests de performance, permet de détecter les problèmes potentiels avant qu’ils ne deviennent critiques. Le remplacement préventif des soupapes, selon les recommandations du constructeur, est une pratique courante pour maintenir la fiabilité du compresseur.
Défaillance des roulements du vilebrequin
Le vilebrequin, pièce maîtresse du compresseur à piston, repose sur des roulements qui supportent des charges importantes. Une défaillance de ces roulements peut avoir des conséquences catastrophiques, allant jusqu’à la destruction complète du moteur. Les causes les plus fréquentes de défaillance des roulements incluent un manque de lubrification, une contamination de l’huile ou un désalignement du vilebrequin.
La surveillance des vibrations est un outil précieux pour détecter précocement les problèmes de roulements. Des analyses d’huile régulières permettent également de vérifier la qualité de la lubrification et de détecter la présence éventuelle de particules métalliques, signe d’une usure anormale. Un entretien rigoureux du système de lubrification et un alignement précis du vilebrequin sont essentiels pour prévenir ces défaillances coûteuses.
Fissures dans le carter moteur
Bien que moins fréquentes, les fissures dans le carter moteur peuvent survenir, notamment sur les compresseurs soumis à des cycles de fonctionnement intensifs ou à des vibrations excessives. Ces fissures peuvent entraîner des fuites d’huile, une perte de compression et, dans les cas extrêmes, une rupture catastrophique du carter.
L’inspection visuelle régulière du carter, associée à des contrôles par ultrasons ou ressuage sur les zones critiques, permet de détecter les fissures naissantes avant qu’elles ne deviennent critiques. Dans certains cas, une réparation par soudure peut être envisagée, mais le remplacement du carter est souvent la solution la plus sûre à long terme.
Problèmes électriques des compresseurs
Les composants électriques des compresseurs sont tout aussi cruciaux que leurs parties mécaniques. Des défaillances électriques peuvent non seulement entraîner des arrêts de production, mais aussi présenter des risques pour la sécurité. Une compréhension approfondie de ces problèmes est essentielle pour assurer un fonctionnement fiable et sécurisé.
Court-circuit du moteur électrique
Le moteur électrique est le cœur du compresseur. Un court-circuit dans les enroulements du moteur peut être causé par une surchauffe prolongée, une infiltration d’humidité ou une détérioration de l’isolation. Ce type de défaillance entraîne généralement un arrêt immédiat du compresseur et nécessite souvent le remplacement complet du moteur.
La prévention des courts-circuits passe par une maintenance régulière incluant des tests d’isolation et des inspections thermographiques. Ces dernières permettent de détecter les points chauds anormaux avant qu’ils ne provoquent une défaillance. L’utilisation de moteurs à haut rendement et de systèmes de protection thermique adaptés contribue également à réduire les risques de court-circuit.
Défaillance du condensateur de démarrage
Le condensateur de démarrage joue un rôle crucial dans la mise en route du compresseur, particulièrement pour les modèles monophasés. Une défaillance de ce composant peut empêcher le démarrage du moteur ou provoquer des démarrages difficiles. Les symptômes typiques incluent un bourdonnement du moteur sans démarrage effectif ou des déclenchements répétés du disjoncteur.
La durée de vie d’un condensateur de démarrage est limitée, en particulier dans des environnements chauds ou lorsque le compresseur effectue des cycles courts fréquents. Un remplacement préventif du condensateur, typiquement tous les 3 à 5 ans selon l’utilisation, peut prévenir de nombreuses pannes. Il est également important de vérifier régulièrement l’absence de signes de gonflement ou de fuite sur le boîtier du condensateur.
Dysfonctionnement du pressostat
Le pressostat est un composant clé qui contrôle les cycles de marche/arrêt du compresseur en fonction de la pression dans le réservoir. Un dysfonctionnement de cet élément peut entraîner des cycles trop fréquents, une surpression dangereuse ou une incapacité à maintenir la pression requise. Ces problèmes peuvent résulter d’une usure mécanique des contacts, d’un encrassement ou d’un déréglage progressif.
Un entretien régulier du pressostat, incluant un nettoyage des contacts et une vérification des réglages, est essentiel pour maintenir un fonctionnement optimal du compresseur. Dans certains cas, l’installation d’un pressostat électronique peut offrir une plus grande précision et fiabilité, notamment pour les applications exigeant un contrôle fin de la pression.
Surchauffe due à une surcharge électrique
La surchauffe du moteur électrique est une cause fréquente de panne, souvent liée à une surcharge prolongée. Cette situation peut survenir lorsque le compresseur fonctionne au-delà de sa capacité nominale, en cas de tension d’alimentation inadéquate ou de problèmes de ventilation. Une surchauffe persistante dégrade rapidement l’isolation des enroulements, conduisant à terme à une défaillance catastrophique du moteur.
La prévention de la surchauffe passe par plusieurs mesures :
- Installation de protections thermiques adaptées
- Surveillance continue de la température du moteur
- Maintien d’une ventilation adéquate autour du compresseur
- Respect des cycles de fonctionnement recommandés par le fabricant
L’utilisation de variateurs de fréquence peut également contribuer à réduire les risques de surchauffe en adaptant la vitesse du moteur à la demande réelle, évitant ainsi les démarrages fréquents et les périodes de fonctionnement à pleine charge prolongées.
Contamination et qualité de l’air comprimé
La qualité de l’air produit par un compresseur est cruciale pour de nombreuses applications industrielles. La contamination de l’air comprimé peut non seulement affecter les processus en aval, mais aussi endommager le compresseur lui-même. Comprendre les sources de contamination et mettre en place des mesures préventives est essentiel pour maintenir l’efficacité et la longévité du système.
Accumulation d’humidité dans le circuit
L’humidité est l’un des contaminants les plus courants dans les systèmes d’air comprimé. Elle provient de l’air ambiant aspiré par le compresseur et se condense lorsque l’air est comprimé et refroidi. Une accumulation excessive d’humidité peut entraîner la corrosion des composants internes, la dégradation des lubrifiants et la formation de givre dans les équipements pneumatiques.
Pour combattre ce problème, plusieurs stratégies peuvent être mises en œuvre :
- Installation de sécheurs d’air adaptés (réfrigérants, par adsorption, etc.)
- Utilisation de purgeurs automatiques sur les réservoirs et les filtres
- Mise en place de séparateurs cycloniques pour éliminer l’eau liquide
- Contrôle régulier du point de rosée de l’air comprimé
Une attention particulière doit être portée au dimensionnement correct des équipements de traitement d’air en fonction du débit et de la qualité requise pour l’application finale.
Colmatage des filtres à air
Les filtres à air d’admission jouent un rôle crucial dans la protection du compresseur contre les particules en suspension dans l’air ambiant. Un colmatage progressif de ces filtres réduit le débit d’air entrant, ce qui peut entraîner une surchauffe du compresseur, une baisse de performance et une usure prématurée des composants internes.
Pour prévenir ces problèmes, il est recommandé de :
- Inspecter régulièrement l’état des filtres à air
- Remplacer les éléments filtrants selon les intervalles préconisés par le fabricant
- Installer des indicateurs de colmatage pour surveiller la perte de charge
- Adapter la fréquence de remplacement à l’environnement d’utilisation du compresseur
Dans les environnements particulièrement poussiéreux, l’utilisation de préfiltres ou de systèmes de filtration multicouches peut significativement prolonger la durée de vie des filtres principaux.
Présence d’huile dans l’air comprimé
La contamination de l’air comprimé par l’huile est un problème fréquent, particulièrement dans les compresseurs lubrifiés. Cette huile peut provenir de fuites internes, d’une défaillance du séparateur huile/air ou d’une saturation des filtres coalescents. La présence d’huile dans l’air comprimé peut avoir des conséquences graves sur les équipements en aval et compromettre la qualité des produits finis dans certaines industries.
Pour minimiser ce risque, plusieurs mesures peuvent être adoptées :
- Utilisation de filtres coalescents haute efficacité
- Maintenance régulière du séparateur huile/air
- Contrôle fréquent des niveaux d’huile et détection des fuites
- Dans les applications critiques, envisager l’utilisation de compresseurs sans huile
L’installation de systèmes de surveillance en continu de la teneur en huile de l’air comprimé peut également permettre une détection précoce des problèmes avant qu’ils n’affectent la production.
Fuites et pertes de pression
Les fuites dans un système d’air comprimé représentent non seulement une perte d’énergie significative, mais peuvent également indiquer des problèmes plus graves au niveau du compresseur ou du réseau de distribution. Identifier et corriger ces fuites est crucial pour maintenir l’efficacité énergétique et les performances du système.
Fissures dans les conduites pneumatiques
Les fissures dans les conduites pneumatiques peuvent survenir en raison de la fatigue des matériaux, de vibrations excessives ou de contraintes mécaniques. Ces fissures, même minimes, peuvent entraîner des pertes de pression importantes et forcer le compresseur à fonctionner plus fréquemment pour maintenir la pression requise.
La détection des fissures nécessite une inspection régulière du réseau, en utilisant des méthodes telles que :
- Tests de pression statique
- Utilisation de détecteurs de fuites à ultrasons
- Application de solutions savonneuses sur les zones suspectes
- Thermographie infrarouge pour détecter les zones de dépressurisation
Une fois détectées, les conduites endommagées doivent être réparées ou remplacées rapidement pour éviter une aggravation du problème et des pertes énergétiques continues.
Joints toriques et raccords défectueux
Les joints toriques et les raccords sont des éléments cruciaux pour maintenir l’étanchéité du système d’air comprimé. Avec le temps, ces composants peuvent se détériorer, entraînant des fuites subtiles mais coûteuses. Les causes fréquentes de défaillance incluent le vieillissement des matériaux, l’exposition à des produits chimiques agressifs ou des températures extrêmes.
Pour prévenir ces problèmes, il est essentiel de :
- Inspecter régulièrement les joints et raccords, en particulier dans les zones soumises à des vibrations
- Utiliser des matériaux adaptés aux conditions d’utilisation (température, pression, environnement chimique)
- Assurer un serrage correct des raccords, sans excès qui pourrait endommager les joints
- Remplacer préventivement les joints toriques lors des opérations de maintenance planifiées
L’utilisation de technologies de détection de fuites, comme les caméras acoustiques, peut grandement faciliter l’identification des fuites mineures avant qu’elles ne deviennent problématiques.
Clapet anti-retour endommagé
Le clapet anti-retour joue un rôle crucial en empêchant le reflux d’air comprimé du réservoir vers le compresseur. Un clapet endommagé ou mal ajusté peut entraîner une perte de pression constante, forçant le compresseur à fonctionner plus fréquemment pour maintenir la pression désirée. Cela augmente non seulement la consommation d’énergie, mais accélère également l’usure du compresseur.
Les signes d’un clapet anti-retour défectueux incluent :
- Une chute de pression rapide lorsque le compresseur est à l’arrêt
- Des démarrages fréquents du compresseur, même en l’absence de consommation d’air
- Des bruits anormaux lors de l’arrêt du compresseur
La maintenance préventive du clapet anti-retour devrait inclure une inspection régulière, un nettoyage et, si nécessaire, un remplacement. Dans certains cas, l’installation d’un clapet anti-retour de qualité supérieure peut offrir une meilleure étanchéité et une durée de vie prolongée.
Pannes liées au système de refroidissement
Le système de refroidissement est vital pour maintenir des températures de fonctionnement optimales dans un compresseur d’air. Des défaillances dans ce système peuvent rapidement conduire à une surchauffe, entraînant des dommages importants et coûteux. Comprendre les points faibles du système de refroidissement est essentiel pour prévenir ces pannes critiques.
Encrassement du radiateur à ailettes
Le radiateur à ailettes est responsable de la dissipation de la chaleur générée par le processus de compression. Au fil du temps, la poussière, l’huile et autres débris peuvent s’accumuler sur les ailettes, réduisant significativement l’efficacité du refroidissement. Cette accumulation peut entraîner une surchauffe du compresseur, une baisse de performance et, dans les cas extrêmes, une défaillance complète du système.
Pour prévenir ce problème, il est recommandé de :
- Effectuer un nettoyage régulier des ailettes du radiateur, en utilisant de l’air comprimé ou des produits de nettoyage adaptés
- Installer des filtres d’admission d’air efficaces pour réduire la quantité de particules atteignant le radiateur
- Envisager l’utilisation de revêtements anti-adhésifs sur les ailettes pour faciliter le nettoyage
Dans les environnements particulièrement poussiéreux, l’installation d’un système de pré-filtration de l’air de refroidissement peut considérablement prolonger les intervalles entre les nettoyages.
Dysfonctionnement du ventilateur de refroidissement
Le ventilateur de refroidissement est un composant critique qui assure la circulation d’air nécessaire pour maintenir des températures optimales. Un dysfonctionnement de ce ventilateur peut rapidement conduire à une surchauffe du compresseur. Les causes courantes de défaillance incluent l’usure des roulements, des problèmes électriques ou des dommages physiques aux pales du ventilateur.
Pour garantir un fonctionnement fiable du ventilateur, il est important de :
- Vérifier régulièrement l’état des pales et l’absence de vibrations anormales
- Inspecter et lubrifier les roulements selon les recommandations du fabricant
- Contrôler périodiquement les connexions électriques et le bon fonctionnement du moteur du ventilateur
L’installation de capteurs de température et de systèmes d’alerte peut fournir une protection supplémentaire en détectant rapidement toute anomalie dans le processus de refroidissement.
Fuite du circuit de refroidissement
Dans les compresseurs refroidis par liquide, les fuites du circuit de refroidissement peuvent avoir des conséquences graves. Non seulement elles réduisent l’efficacité du refroidissement, mais elles peuvent également entraîner une contamination de l’huile ou de l’air comprimé. Les fuites peuvent survenir au niveau des joints, des raccords ou des échangeurs de chaleur, souvent en raison de la corrosion, des vibrations ou du vieillissement des matériaux.
Pour prévenir et détecter les fuites du circuit de refroidissement :
- Effectuer des inspections visuelles régulières des composants du circuit
- Surveiller le niveau de liquide de refroidissement et rechercher toute baisse inexpliquée
- Utiliser des additifs de détection de fuites fluorescents dans le liquide de refroidissement
- Réaliser des tests de pression périodiques sur le circuit fermé
En cas de détection d’une fuite, il est crucial d’identifier et de réparer rapidement la source pour éviter des dommages plus importants au compresseur.
Maintenance préventive et diagnostics
La maintenance préventive et les techniques de diagnostic avancées sont essentielles pour maximiser la fiabilité et la durée de vie des compresseurs d’air. En adoptant une approche proactive, il est possible de détecter et de résoudre les problèmes avant qu’ils ne deviennent critiques, réduisant ainsi les temps d’arrêt et les coûts de réparation.
Analyse vibratoire pour détecter les défauts précoces
L’analyse vibratoire est un outil puissant pour détecter les problèmes mécaniques à un stade précoce. Cette technique permet d’identifier des anomalies telles que le désalignement, le déséquilibre, l’usure des roulements ou les problèmes de transmission avant qu’ils ne causent des dommages importants.
Pour mettre en œuvre efficacement l’analyse vibratoire :
- Établir une ligne de base des signatures vibratoires du compresseur en bon état
- Effectuer des mesures régulières et comparer les résultats à la ligne de base
- Utiliser des capteurs de vibration permanents pour un suivi continu sur les équipements critiques
- Former le personnel de maintenance à l’interprétation des données vibratoires
L’analyse des tendances vibratoires permet non seulement de détecter les problèmes, mais aussi de planifier les interventions de maintenance de manière optimale.
Contrôle régulier de la qualité de l’huile
L’huile joue un rôle crucial dans le fonctionnement et la longévité d’un compresseur. Une analyse régulière de l’huile peut révéler de nombreuses informations sur l’état du compresseur, y compris l’usure des composants, la contamination et la dégradation de l’huile elle-même.
Un programme d’analyse d’huile efficace devrait inclure :
- Des prélèvements réguliers d’échantillons d’huile pour analyse en laboratoire
- La surveillance des niveaux de particules métalliques, indicateurs d’usure des composants
- L’évaluation de la viscosité et de l’acidité de l’huile pour déterminer sa durée de vie restante
- La détection de contaminants tels que l’eau ou les particules abrasives
En interprétant correctement ces données, il est possible d’optimiser les intervalles de vidange et de détecter précocement les problèmes mécaniques.
Inspection thermographique des composants électriques
La thermographie infrarouge est une technique non invasive permettant de détecter les points chauds anormaux dans les systèmes électriques. Cette méthode est particulièrement utile pour identifier les connexions desserrées, les surcharges ou les déséquilibres dans les circuits électriques du compresseur.
Pour tirer le meilleur parti de l’inspection thermographique :
- Établir un programme d’inspection régulier, en particulier pour les composants critiques
- Former le personnel à l’utilisation correcte des caméras thermiques et à l’interprétation des images
- Documenter et suivre l’évolution des points chauds détectés au fil du temps
- Agir rapidement sur les anomalies thermiques identifiées pour prévenir les pannes
La thermographie peut également être utilisée pour surveiller l’efficacité du système de refroidissement et détecter les fuites dans les circuits pneumatiques.
Utilisation de capteurs IoT pour la surveillance en temps réel
L’Internet des Objets (IoT) offre de nouvelles possibilités pour la surveillance et la maintenance prédictive des compresseurs d’air. Des capteurs connectés peuvent collecter en continu des données sur divers paramètres de fonctionnement, permettant une détection précoce des anomalies et une optimisation des performances.
Les avantages de l’utilisation de capteurs IoT incluent :
- La surveillance en temps réel des températures, pressions, vibrations et consommation électrique
- L’analyse automatisée des données pour détecter les tendances et prédire les pannes potentielles
- L’optimisation des performances en ajustant les paramètres de fonctionnement en fonction des conditions réelles
- La réduction des coûts de maintenance grâce à une planification plus précise des interventions
L’intégration de ces technologies dans une stratégie globale de maintenance prédictive peut significativement améliorer la fiabilité et l’efficacité des systèmes d’air comprimé.